EIN
KOMPAKTER ÜBERBLICK
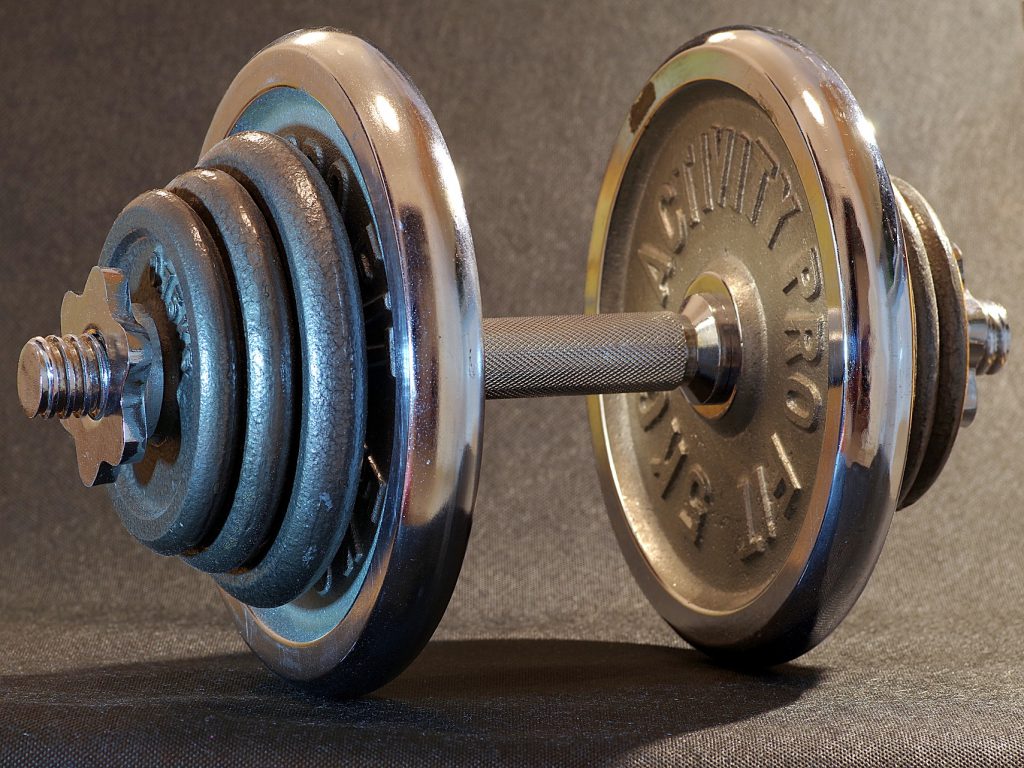
Nachfolgend wollen wir auf Sensoren eingehen, die Messgrößen aus der sog. Dynamik erfassen. Hierzu gehören zunächst Kraft, Druck und Drehmoment. Abschließend gehen wir noch auf die Messung des Durchflusses einer Flüssigkeit oder eines Gases in einem Rohr bzw. Schlauch ein. Der Durchfluss ist zwar eine kinematische Messgröße, wird jedoch i.d.R. indirekt über dynamische Effekte gemessen.
Kraftsensoren
Auch wenn es bei Kraftsensoren wie bei allen Sensorarten sehr viele unterschiedliche Funktionsprinzipien gibt, nach denen diese aufgebaut sind, so dominieren doch zwei Grundverfahren das Angebot: DMS-basierte Kraftsensoren sowie solche nach dem piezoelektrischen Prinzip. Das Bild zeigt ausgewählte Varianten des erstgenannten Typs.
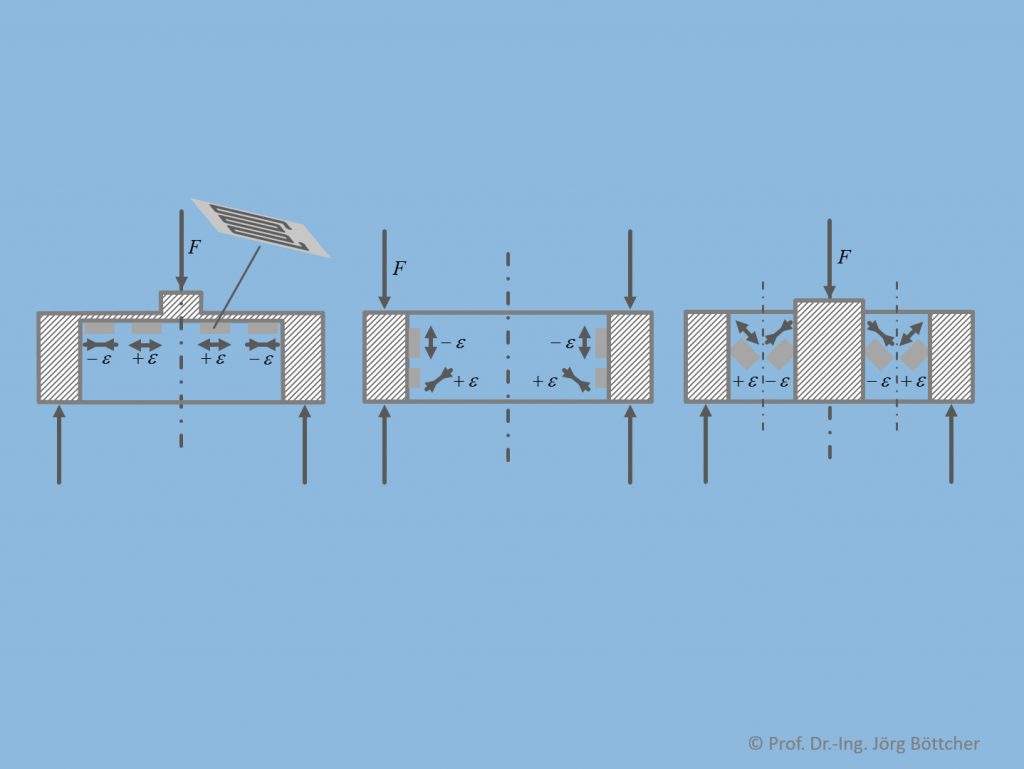
DMS-Kraftsensoren
In je nach Kraftmessbereich entsprechend ausgehölten massiven Zylindern sind Dehnungsmessstreifen aufgeklebt, die gedehnt bzw. gestaucht werden. Sie verändern hierbei ihre ohmschen Widerstände, was meist durch nachfolgende Brückenschaltungen in elektrische Spannungssignale gewandelt wird.
Kraftsensoren, die speziell Wägezwecken dienen, werden alternativ meist „Wägezellen“ genannt. Sie werten formal die Gewichtskraft aus. Die für die Umrechnung in die eigentlich gewünschte Masse erforderliche Erdbeschleunigung ist bekanntermaßen von der genauen Position auf der Erde abhängig, weshalb man Systeme mit derartigen Wägezellen lokal kalibriert.
Piezoelektrischen Kraftsensoren verwenden Quarze, die bei Druckausübung Ladungsträger freisetzen. Ein Basissensorelement besteht dabei zunächst aus einem entsprechend geschliffenen Quarz mit zwei Elektrodenflächen vergleichbar einem Kondensator. Im Kraftsensor des unteren Bildes sind Quarz und Elektroden als komplett umlaufende Bahn ausgeführt. Außerdem ist nicht nur ein Basissensorelement verbaut, sondern zwei übereinander angeordnete mit gegensinniger elektrischer Orientierung und gemeinsamer Mittelelektrode. Links am Sensorgehäuse ist ein Koaxialkabel angedeutet, wie es typischerweise verwendet wird. Die Mittelelektrode ist auf den Innenleiter dieses Kabels geführt, während dessen Außenleiter über die metallischen Gehäuseelemente mit den beiden anderen Quarzelektroden verbunden ist. Die zwei Basissensorelemente sind also elektrisch parallel geschaltet, wodurch sich die Ladungsträgerfreisetzung bei Krafteinwirkung verdoppelt. Mechanisch sind sie in Serie geschaltet und sehen dieselbe Kraft F.
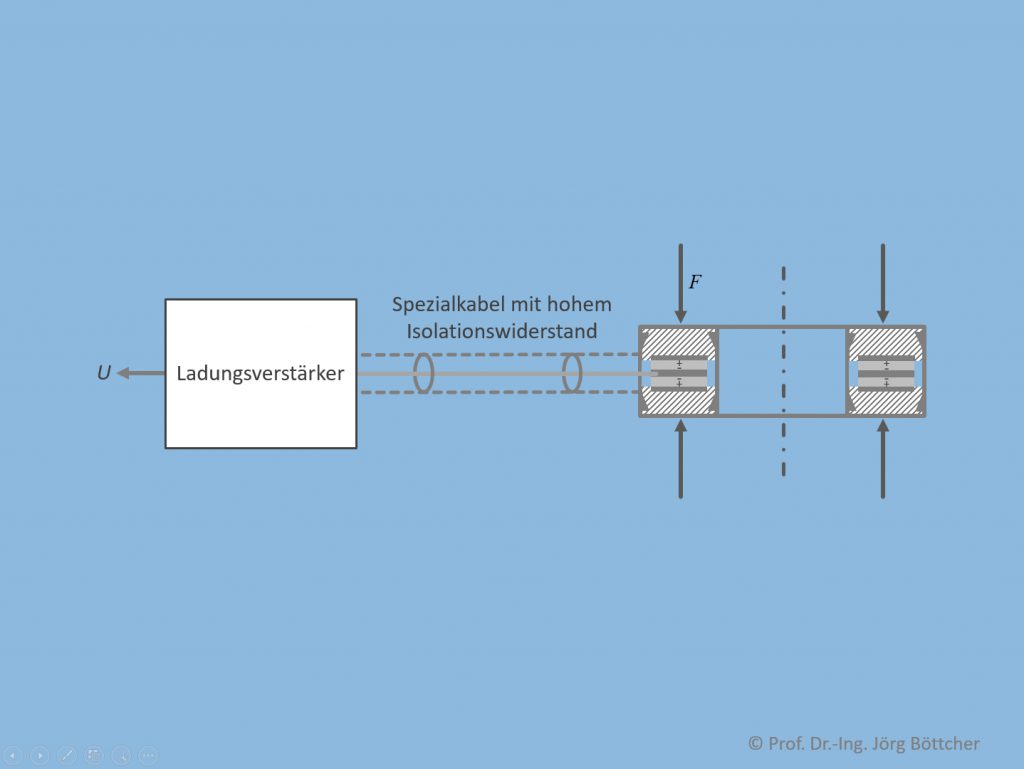
Piezoelektrischer Kraftsensor mit Ladungsverstärker
Die Hersteller von piezoelektrischen Sensoren bieten sog. Ladungsverstärker an, die über das Koaxialkabel mit dem Sensor verbunden werden. Dabei handelt es sich um eine spezielle Integratorschaltung, die aufgrund ihres sehr niedrigen Eingangswiderstands sämtliche freigesetzten Ladungsträger sofort „absaugt“, auf einem internen Kondensator abspeichert und die dabei aufgebaute Spannung ausgibt.
Unter dem Kürzel IEPE (Integrated Electronics Piezo Electric) haben Hersteller einen übergreifenden Standard für Piezosensoren spezifiziert, die bereits über einen im Sensorgehäuse integrierten Ladungsverstärker verfügen. Das auch hier als Koaxialkabel ausgeführte Messkabel dient zusätzlich zur Konstantstromversorgung der Sensorelektronik.
Drucksensoren
Sensoren zur Messung des Drucks in Gasen oder Flüssigkeiten werden in aller Regel so gebaut, dass das druckführende Medium auf eine im Sensor befindliche Membran wirkt. Die Membranauslenkung kann dabei z.B. indirekt über entsprechend angebrachte DMS erfasst werden. Eine weitere Variante arbeitet kapazitiv. Die in diesem Fall stets leitfähige Membran bzw. alternativ auch eine an der Membran befestigte metallische Platte o.ä. bildet zusammen mit einer feststehenden Platte einen Kondensator, dessen Kapazität sich in Abhängigkeit vom durch den Druck beeinflussten Abstand ändert. Eine dritte Version schließlich basiert auf einem piezoelektrischen Sensorelement. Die mit einem Druck beaufschlagte Membran drückt dabei mit einer sich dazu proportional aufbauenden Kraft auf das Sensorelement, was zu entsprechender Ladungsfreisetzung führt.
Drehmomentsensoren
Drehmomente werden i.d.R. an rotierenden Wellen gemessen, um deren Belastung zu überwachen. Hierzu gebräuchliche Drehmomentsensoren basieren auf einer Anordnung gemäß nachfolgendem Bild. Der Sensor wird über entsprechende Ankoppelelemente in die Welle montiert. Das von der Antriebsseite zur Lastseite übertragene Drehmoment M wird im Mittelteil des Sensors mit verschiedenen Messmethoden ermittelt. Drehmomentsensoren heißen häufig auch Drehmomentwandler bzw. in einer speziellen flachen Bauweise mit externer Elektronik auch Drehmomentmessflansch.
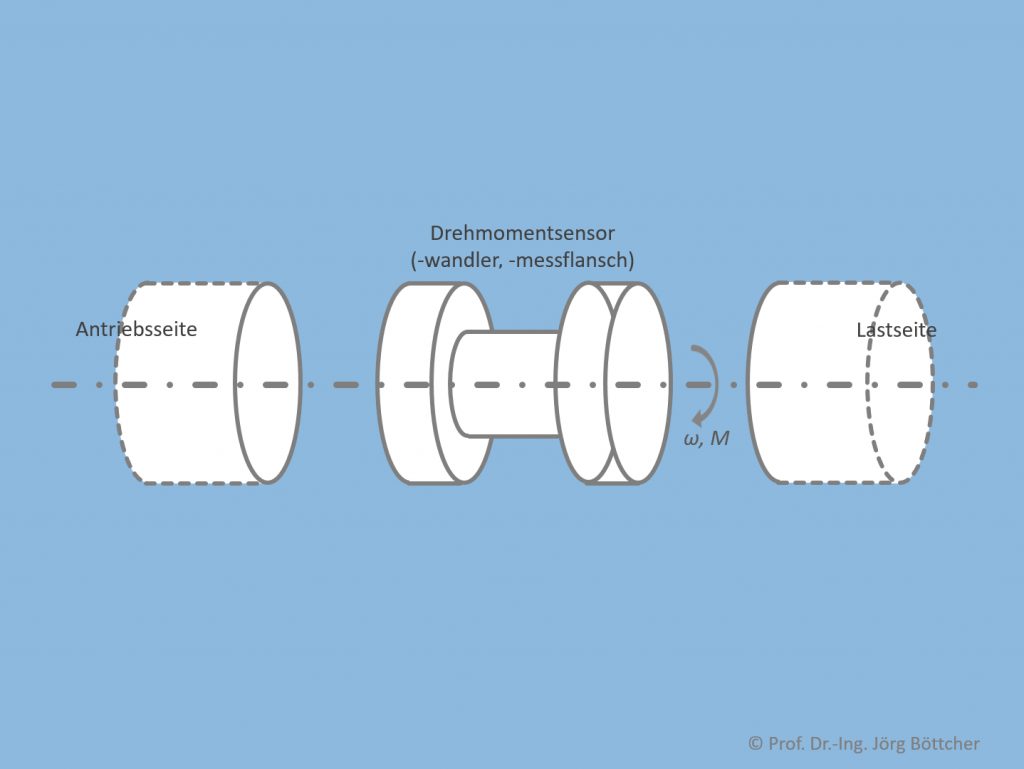
Anordnung eines Drehmomentsensors in einer Welle
Es dominieren zwei Messmethoden: Bei einer sind vier DMS so angebracht, dass sie die im Zuge der Verwindung auftretenden Dehnungen bzw. Stauchungen an der Oberfläche erfassen. Bei der anderen sind sensorintern entsprechend schlüssig angebrachte piezoelektrische Sensorelemente vorhanden, auf die Schub- bzw. Schereffekte wirken.
Unabhängig von der konkret verwendeten Messemethode muss der Sensorhersteller dafür sorgen, dass die rotierenden Sensorelemente mit nachgeschalteten nichtrotierenden Auswertesystemen signaltechnisch verbunden werden, was heute meist funktechnisch erfolgt. Vor allem bei größeren Wellen wie z.B. Schiffsantriebswellen können keine fertigen Drehmomentsensoren installiert werden. Dort werden dann meist Lösungen mit spezifisch verklebten DMS inkl. zugehöriger Messelektronik realisiert.
Durchflusssensoren
Durchflusssensoren messen die Menge einer Flüssigkeit oder eines Gases, die pro Zeit durch ein Rohr- oder Schlauchsystem fließt. Sie müssen deshalb – von speziellen Messverfahren abgesehen, die eine Montage außerhalb bestehender Rohre ermöglichen (eines werden wir unten noch ansprechen) – in das Rohr- bzw. Schlauchsystem installiert werden. Je nach Messverfahren ermitteln Durchflusssensoren den Volumendurchfluss in der Einheit m3/s (bzw. oftmals z.B. als l/min angegeben) oder den Massendurchfluss in kg/s. Eine Umrechnung ist grundsätzlich über die Dichte ρ gemäß
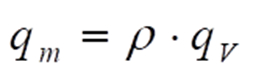
möglich.
Wir wollen nachfolgend ein paar sehr weit verbreitete Messverfahren im Überblick ansprechen, wie sie bei Durchflusssensoren eingesetzt werden:
Beim Turbinenradzähler wird der Durchfluss in eine dazu proportionale Drehzahl umgesetzt, welche mit Methoden der Drehzahlmessung ausgewertet wird.
Das sog. Wirkdruckverfahren basiert darauf, dass eine in den Strömungsfluss eingebrachte Engstelle zu einer höheren Partikelgeschwindigkeit führt, die mit einem Abfall des seitlich zu entnehmenden sog. statischen Drucks im Vergleich zum Druck an einer Stelle zuvor verbunden ist. Die beiden Drücke werden mit üblichen Drucksensoren gemessen.
Ein Verfahren, das den Halleffekt ausnutzt, funktioniert nur, wenn das strömende Medium zumindest in gewissem Maße elektrisch leitfähig ist, also freie Ladungsträger aufweist. Unter Magnetfeldeinwirkung werden diese auf eine von zwei seitlich gegenüber angebrachten Kondensatorplatten abgelenkt, was zu einer elektrischen Spannung führt. Das Verfahren wird meist mit dem Kürzel MID bezeichnet (Magnetisch-induktive Durchflussmessung).
Ein weiteres Verfahren basiert auf der Aussendung und dem Empfang von Ultraschallsignalen. Sendet man einen Ultraschallimpuls in Strömungsrichtung („abwärts“) unter einem gewissen Winkel quer von einer auf die andere Rohrseite, so ist dessen Ausbreitungsgeschwindigkeit von der Teilchengeschwindigkeit im Medium und damit vom Volumendurchfluss abhängig. Zur Elimination der meist nur ungenau bekannten Schallgeschwindigkeit hierbei verbaut man in der Praxis meist eine zweite Ultraschallstrecke direkt daneben, bei welcher ein Ultraschallimpuls strömungsaufwärts ausgestrahlt wird.
Beim Wirbelzähler wird ein Staukörper in die Strömung eingebracht. An dessen Außenkanten bricht die Strömung periodisch immer wieder ab, was zur Ablösung entsprechender Wirbel führt. Die Frequenz, mit der dies geschieht, ist proportional zum Volumendurchfluss und kann durch entsprechend geeignete Verfahren ermittelt werden.
Der thermische Massenstrommesser basiert auf der Abkühlung eines im strömenden Medium befindlichen ohmschen Widerstand, der durch einen Heizstrom aufgeheizt wird. Bei älteren Sensoren hat man hierfür einen Draht mehrmals quer zur Strömungsrichtung gespannt (sog. Hitzdraht-Anemometer). Heute verwendet man meist flächige Widerstandselemente als Teil eines in MEMS-Technologie (Micro Electro Mechanical System) aufgebauten Sensors. Die Abkühlung bewirkt eine Widerstandssenkung, welche schaltungstechnisch ausgewertet wird.
Der Massenstrom kann auch mit dem Coriolisverfahren gemessen werden (siehe unteres Bild). Das strömende Medium wird hierbei innerhalb des Sensors über ein beispielsweise U-förmig gebogenes Rohr geführt. Das Rohraußenstück wird typischerweise über elektromagnetische Anregung in eine nicht sehr große sinusförmige Auf- und Abschwingung versetzt. Zur Minimierung des Strombedarfs zur Anregung wählt man häufig die Resonanzfrequenz des Rohrstücks. Bei Massenfluss wirken nun Corioliskräfte auf die Masseteilchen, die sich zum Rohraußenstück hin bewegen bzw. von diesem zurück, jeweils in unterschiedlicher Richtung. Diese führen dazu, dass das Rohr periodisch mit der Anregefrequenz verwunden wird, was sich in einem entsprechend periodisch schwankenden kleinem Torsionswinkel äußert. Je nach Hersteller wird im Sensor z.B. die Amplitude des Torsionswinkels oder die Phasenverschiebung der Rohrschwingung in Bezug auf die Anregeschwingung ausgewertet.
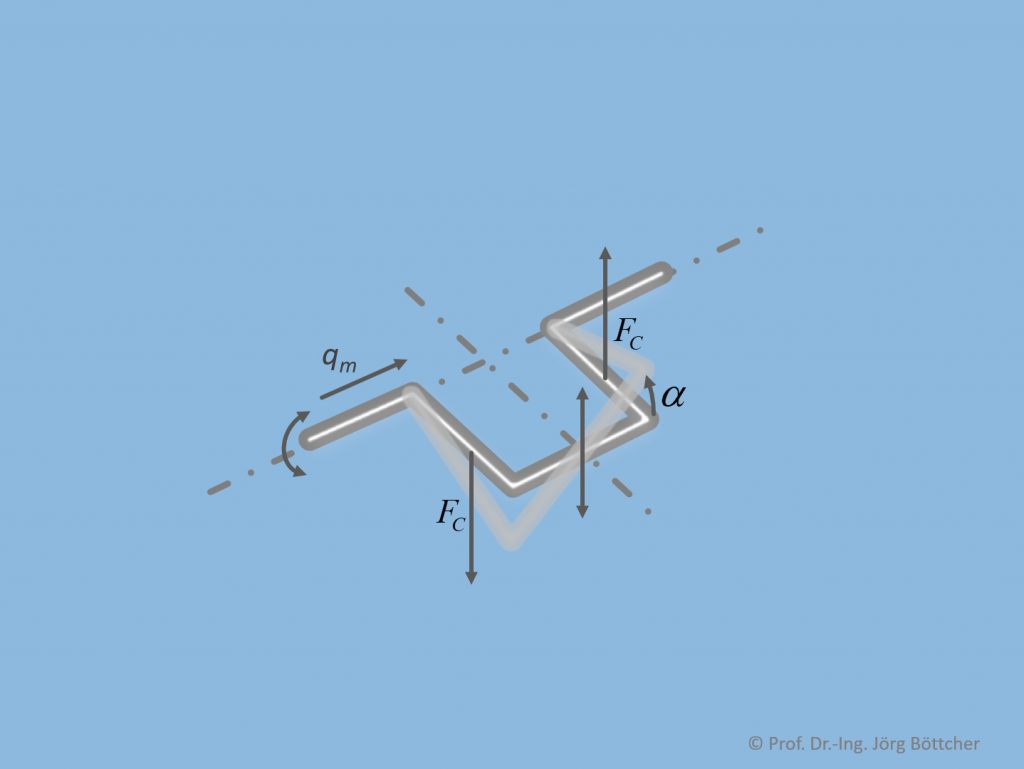
Messung des Massendurchflusses mit Coriolisverfahren
WENN SIE ES GENAUER WISSEN WOLLEN: